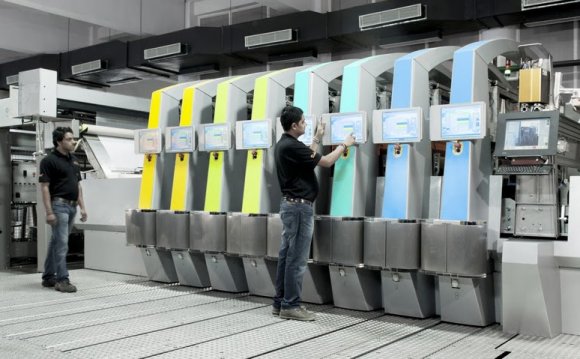
By Andrew Lewis
Occasionally We have recommended for a textile task, but I have put off by the looked at trawling through apparently endless bolts of fabric during the store. Then I look at the hassle of haggling across price and ending up with 3 times as much fabric as I really needed.
I decided to use printing my very own fabric on an inkjet printer, therefore the results really exceeded my objectives. The advantages to the method tend to be great, and I don’t need certainly to haggle over costs any more.
I have my personal designs, into the volume i would like, at a fraction of the cost i'd normally spend. Truly the only drawback is the fact that individuals keep asking me to print one thing special for all of them, also!
About Ink
Printing your own fabric is not as difficult because appears, and you don’t need any special gear to get started. Really the only key to a successful printing is make sure that you have the right style of ink. Low priced printer cartridges and refills often use a dye-based ink that colors unpredictably on textile, that will also wash out totally in liquid.
More costly printer cartridges use pigment ink. Pigment ink is colorfast on many different surfaces, and it is much more useful for printing on fabric.
Regrettably, finding out if you have pigment ink or dye just isn't always direct. Your printer handbook is an excellent place to start, and a physical study of the ink should settle the matter certainly. If the printer cartridges need changing, remove the yellow ink and put some on an item of glass. Yellow pigment ink should be radiant but opaque, while yellow-dye should be transparent and virtually brown in shade.
Disclaimer: Not all printers can print on fabric, and putting fabric through your printer could damage it permanently. That is an experimental method, and you should only check it out in the event that you recognize that it involves some risk.
Products
Light-colored textile
Printer that utilizes pigment inks
Scissors
Card
Gluey tape
Directions
Step 1: Choose a light-colored, level textile, and slashed it towards maximum width that your particular printer are designed for. I have an Epson R1800, so that it can take just over A3+ circumference of material. If the printer aids publishing from a roll, then you can certainly result in the fabric so long as you fancy. Or else you will need to cut the fabric into sheets. If you use a lengthy length of textile, you might want to move it onto a cardboard pipe making it much more workable.2: simply take an item of card similar width as fabric and fix the end of fabric on card utilizing gluey tape. The card works like a leader, giving the printer something to keep onto when you first begin printing. I personally use a piece of card about 10″ lengthy, and tape the textile about 2″ in through the end. When the card is through the printer, the weight will help keep carefully the fabric operating smoothly.
Step 3: Feed the card into the printer. Regarding the Epson R1800, I use the roll feed to accept the report, since the paper goes into the printer at a far more superficial angle also because i will print endless lengths utilizing the banner mode of printer.
Step: make your design on the computer, and print it. Keep a consistent attention in the printer while it is operating, watching that material doesn’t get creased or jam up the pinnacle. Should you have a problem, turn the printer off within wall surface and obvious the material manually before restoring power. Do not pull or move the textile even though it is nevertheless being printed. Small alterations in fabric stress can make your design distort, and increase the chance of creases creating.
Step 5: you will have to fiddle around because of the brightness / shade settings on the printer to obtain the design searching right. Each material is slightly various, and experimentation is absolutely required if you would like get great results.
Step 6: When the publishing is completed, you really need to leave your custom fabric to dry for approximately one hour. You will probably find that a number of the ink comes down on your arms when you first deal with the fabric. This is normal, and is nothing to be concerned about. Merely rinse the material in tepid to warm water to get rid of any extra pigment, and hang it to dried out.
Action 7: When the fabric is dried out, iron the reverse part at low-temperature. With this point onwards, the material can usually be treated similar to shop-bought fabric. I will suggest using a very good clean and ironing in the reverse part in which feasible to aid preserve the colors.
About the creator:
Andrew Lewis is a journalist, a maker, an ardent victophile, as well as the president of this web log. He's presently studying for a PhD. in archaeometrics and 3D checking at University of Wolverhampton.