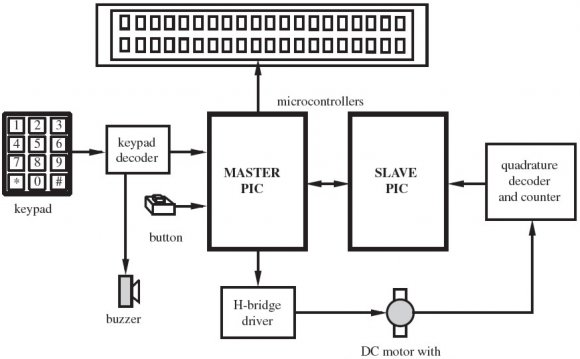
Open Access
So that you can develop a ceramic element by inkjet publishing, the object must be fabricated through interacting with each other and solidification of drops, typically into the array of 10−100 pL. To experience this goal, stable porcelain inks should be created. These inks should fulfill particular rheological conditions that may be illustrated within a parameter area defined because of the Reynolds and Weber figures. Printed drops initially deform on impact with a surface by dynamic dissipative processes, but distribute to an equilibrium form defined by capillarity. We are able to recognize the procedures by which these drops communicate to create linear features during publishing, but there is a poorer level of understanding as to how 2D and 3D structures form. The security of 2D sheets of ink seems to be possible over an even more restricted variety of process problems that is seen using formation of lines. In most cases, the ink solidifies through evaporation and there is a necessity to regulate the drying out process to eliminate the: “coffee ring” defect. Despite these uncertainties, there has been most reports in the successful use of inkjet printing for the manufacture of little porcelain components from several different ceramics. This method provides great leads as a future production strategy. This review identifies possible places for future research to improve our comprehension of this production strategy.
KEYWORDS
- additive make;
- 3D publishing;
- inkjet printing;
- porcelain components
1. Introduction
Inkjet printing ended up being one of the first technologies become created for additive manufacture. In 1992, Sachs et al. at MIT described a way for production porcelain casting cores and shells by inkjet printing a binder phase onto a ceramic powder bed . The binder stage acts as an adhesive, collectively joining the porcelain powder where it's imprinted, and leaving free unconsolidated powder in other places. As soon as a layer was printed, the powder sleep is decreased and new dust is applied. This brand new level has an additional binder design printed about it. An object is printed by saying this method of lowering, incorporating fresh dust, and binder printing. The final printed item may be taken from the unconsolidated powder prior to last sintering, if needed. This methodology features became extremely versatile, and has been created with brand new materials beyond those in its initial application idea. These days, additive make by inkjet printing has actually programs in biomaterials, useful ceramics, as well as other areas. It's generated a low-cost means for the rapid fabrication of models, including very successful commercialization.