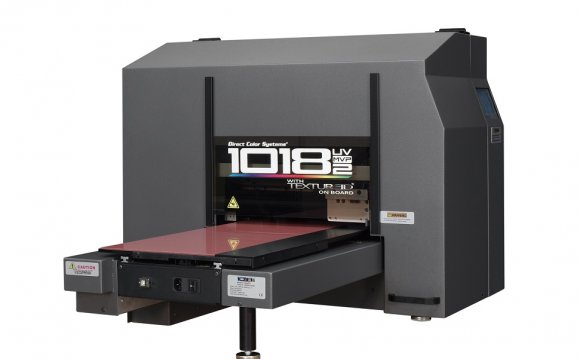
It’s been an only couple of weeks since we brought you a quick contrast between two of the very most used 3D publishing technologies, Selective Laser Sintering or SLS and Stereolithography or SLA. This time around we are going to address some doubts regarding Polyjet 3D printing and how it compares to SLS just like we did earlier in the day. Here is our SLS vs Polyjet contrast!
As you may keep in mind from our final contrast, SLA printers tend to be -by design- unable to print with over one product at the same time, pushing an individual to construct any help structure required using the exact same material useful for the imprinted item, which most of the time contributes to undesired scars in the object’s area. Even if assistance structures are not required, occasionally the job only needs several product to be able to display numerous colors or technical properties and that by itself would leaves SLA printers out of the online game. Planning to over come these limits while maintaining the superb quality offered by SLA, Objet Geometries Ltd ( these days merged with Stratasys) developed Polyjet 3D printing technology in 2007. In some aspects it may be however while the union of two ripped and matured technologies back then and today: SLA 3D Printing and regular inkjet “2D” publishing.
Credit: Stratasys
In the same way an example, imagine you just printed some shape from the regular inkjet printer which you have actually home. Millions of microscopic ink droplets had been jetted into the paper’s area forming that shape which you wished to printing. Due to the paper’s porosity all the ink is soaked up.
In the event that you did this once more on a watertight system the ink layer could have a particular depth over the area, as soon as it dries up you could duplicate the method stacking another level of ink and doubling the total depth. Change”thickness” for “height” and there you are going, you're now 3D publishing!
Since drying up ink does take time, Objet’s designers hang on this idea but utilizing quickly healing photopolymers instead of ink and added a few powerful Ultraviolet LEDs right by the polymer injectors in order to rapidly solidify the jetted polymer. Additionally motorized the injectors check out move horizontally (2D) and the printing system vertically (1D) to eventually be able to place a droplet anywhere on a specific 3D area.
Selective Laser Sintering (SLS)
Sintering involves compacting and forming a good size of product by heat and/or pressure without melting it to the point of liquefaction. The raw material on a SLS 3D printer comes as a thin powder of either synthetic (typically Nylon) or a plastic established mix with aluminum, cup, carbon fibers or any other materials. A thin layer if this powder is placed from the publishing sleep, inside a hot chamber because of the temperature just underneath the plastic’s sintering point. Which means that the plastic particles simply need a small rise in temperature to stay for their nearest neighbors forming an excellent thin sheet of plastic. This heat kick-up is created because of the infrared laser that rapidly scans over all the 2D section of the thing being printed before a layer of plastic dust is used additionally the procedure begins again, each level staying with usually the one underneath. After every one of the layers were completed, the thing is uncovered through the unsintered dust volume and cleaned.
Resolution
Just as we stated on our final comparison (link at the conclusion of this informative article!) we could only discuss typical resolution values of these two technologies, as every person printer need unique specs.
Layer width on SLS 3D printers is normally on the 50-150µm range, because of the horizontal quality based highly regarding the design it self, but often in the 200-300µm range. For example, if you print a vertical through-hole the minimal diameter resoluble depends on its height.
On Polyjet 3D printers each layer can be as thin as 15µm even though it’s usually around 30µm, for increased rate. Because takes place with SLS printers, horizontal quality is gloomier becoming regarding the 100-200µm range.
Keep in mind these values mean that a printer can actually produce a feature of that size, with a form written by the type of this procedure being used. If you desired to reproduce a 15x50x50µm completely rectangular field, you'll require a resolution method above that of the printer to eliminate the razor-sharp angles. For a Polyjet printer, the “building bricks” tend to be droplets, maybe not rectangular cardboard boxes, and that is the key reason why you can not print precisely at a micron scale.
Mechanical properties
Both SLS and Polyjet 3D printers may use many products, typically polyamide based substances for SLS and resins for Polyjet, thus we are restricted to a general description of technical properties available.
The polyamide (PA) utilized by SLS printers is common as Nylon. This product has attained its reputation for becoming an extremely versatile product and simply put, a beneficial all-rounder. it is really strong and just versatile adequate to not ever break under way too much load, it’s inexpensive and meals appropriate. By the addition of products like metal, carbon dietary fiber, glass or unique chemical substances together with the PA dust producer can alter mechanical properties along with other properties such as shade, reflectiveness, fire weight, etc.
Polyjet resins can be bought in several colors, rigid and rubber-like, opaque and clear. Whereas the most basic printers may use only one resin at a time, producing single-material items, the greater amount of modern-day and higher level (and high priced) printers can dynamically blend two or three resins during publishing process, successfully “creating” the publishing material for each individual polymer jet. This enables an individual having different colors, flexibilities and even transparent materials all-in exactly the same object without a multiple part assembly and gives this technology and benefit against various other 3D printing technologies. If support material ended up being necessary for an intricate form, one of the resins are a gel-like resin that can be effortlessly removable with liquid following the print is finished.
Surface
Despite to be able to make use of a few products with a SLS printer, the item will be solitary product. Regardless the material selected, the top of an object developed by sintering powder is always somewhat rough, comparable to a sanded surface. This is because the powder’s particles are not totally melt but just sintered plus some regarding the microscopic granularity associated with the dust remains on object’s surface. This isn't one thing you can easily see aided by the naked eye, however it could be thought with the nail.