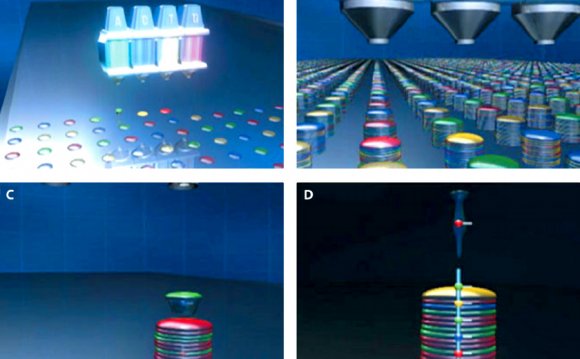
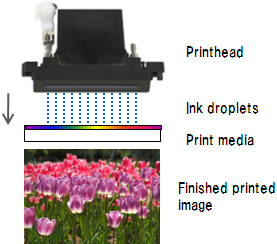
About Inkjet
Inkjet technology utilizes tiny ink droplets to facilitate direct printing without the unit entering connection with the printed surface. Because this technology allows non-contact printing, it can be applied to all kinds of media and it is now-being introduced to be used in an array of fields including general-purpose to professional. The simple structure that combines the inkjet printhead with the scanning apparatus offers the merit of maintaining device expenses down. Besides, simply because they require no dishes, inkjet printers deliver advantage of significant cost savings in publishing put up time versus standard printing methods that want a set printing block or plate, etc. (example. screen publishing).
Scan publishing and Single-pass printing
There's two types of inkjet printing systems: scan printing and single-pass printing. In scan printing, the printhead carriage reciprocates within the sub-scanning way (laterally according associated with print news), making a number of passes to complete the picture printing procedure. In single-pass printing, the printhead carriage remains in a hard and fast place and finishes picture printing in one pass as the print product is conveyed underneath. For their high-speed printing ability, single-pass systems are coming into use within the world of professional publishing where high efficiency is needed.
3-cycle Drive Printhead
Konica Minolta's on-demand piezo printhead employs 3-cycle drive technology that provides energy-conserving benefits. This technology divides nozzles into three groups for timed ink-ejection control. Because this approach features a structure enabling large nozzle density, it's effective inside growth of high-image high quality inkjet printheads.
Konica Minolta Printhead Construction
Printhead Structure (Nozzle surface)
3-cycle drive head concept
Firstly, ink is ejected from channel-A to make an element of the image.
Next, after ejection from channel-A, ink is ejected from channel-B to make the image.
After ejection from channel-B, ink is ejected from channel-C to perform the image.
Decrease in energy intake to about 50per cent
Compared to the past KM512 Series, the KM1024 Series, that has been launched onto the market last year, features an even more small building to comprehend a decrease in energy usage of approximately 50per cent. Development of a new structure has made it possible to reduce the ink station length and lower capacity, causing an important reduction in energy consumption. Energy preservation, a merit of this piezzo system, has been further improved.
Comparison of new (right) and current (left) architectures
Tall Durability for Industrial Applications
Industrial applications require using all sorts of inks. Durable elements and optimum products have now been selected to satisfy the requirements of all kinds of inks from low-viscosity types particularly liquid based inks to high-viscosity kinds particularly UV cured inks.
Precision Processing and Assembly Tech
Precision processing technology (example. laser processing, dicing handling and product processing), among Konica Minolta's core technologies, tends to make accuracy handling and system of the primary components and products for the printhead feasible. Besides, our outstanding fully-automatic all-nozzle ejection overall performance assessment technology assists you to recognize mass-production of top-notch products and establish a production system effective at fast offer.
Share mode Piezo Inkjet Printhead
Konica Minolta inkjet minds can handle a wide range of inks to meet the requirements of various manufacturing programs. The principle of shear mode piezo actuation with shared wall surface framework enables reduced energy usage in addition to a high-density nozzle range.
On-demand dot dimensions modulation, often called grey-scale mode, allows the printing of top-notch photos and functions to improve productivity. All development tasks are based on advanced computer system simulation strategies that can precisely anticipate the droplet formation procedure caused by differential ink traits.
The concept of ink ejection
Micro scale stations created from piezo electric material are created to contract by the application of an electric fee. As stations agreement, ink included in the station is forced out through the nozzle as a droplet. While the channel comes back its initial condition, capillary activity causes ink to move into the station which makes it ready to create next drop.
*Orage indicates pressurized condition. Blue shows depressurized state.Textile Printer Ink
The textile printer inks created for Nassenger Series are designed to meet up with the greatest requirements globally regarding environmental protection and human being health.
Dispersed dye inks suitable for polyester and acetate can be found, since tend to be reactive inks for many substrates including cotton, silk and wool.
Dispersed Dye | Reactive | |
---|---|---|
Cotton Fiber | NA | Excellent |
Rayon | ||
Hemp | Great | |
Silk | ||
Wool | ||
Nylon | ||
Polyester | ||
Acetate |

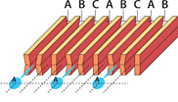

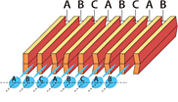